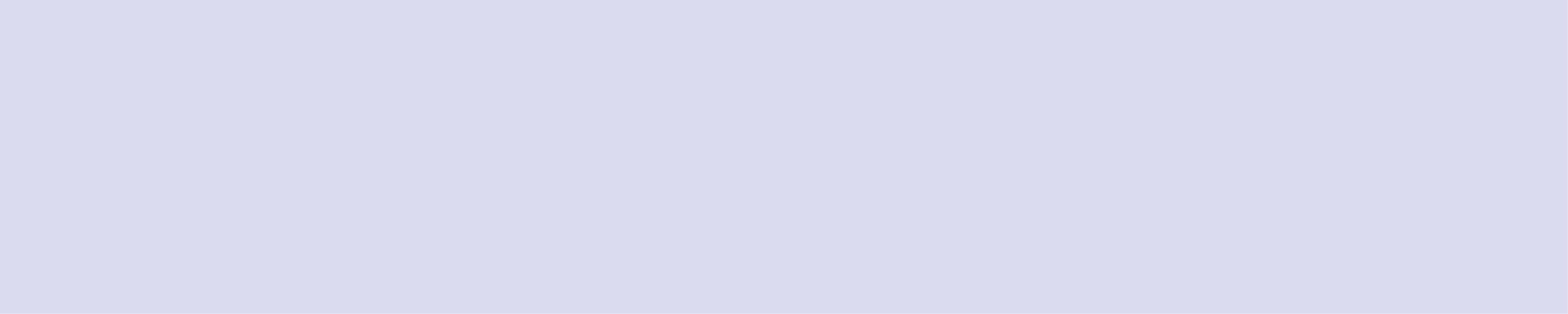
Vermont institutions, hunger relief organizations, restaurants, and food retailers are limited in the amount of fresh, whole Vermont produce they can purchase, due to increasing food service labor shortages and the difficulty and cost of working with seasonal, perishable, and irregularly shaped produce. To limit the loss of this market share to out-of-state producers, Vermont processing facilities have begun to sell cut and frozen locally grown vegetables, but issues of capital, infrastructure, logistics, and communication have limited their expansion potential. Collaboration between producers, processors, and buyers, substantial infrastructure investments, and policies to support producer and processor expansion are needed to encourage in-state minimal processing and continue the growing momentum of local purchasing.
Vermont institutions are interested in Vermont produce, but this demand is often misaligned with the quantity, variety, and seasonality of fresh produce (see College and Hospital Procurement brief, School Food Procurement brief). There are a number of logistical barriers to address such as food service labor shortages (resulting in insufficient time and capacity to process vegetables on-site), difficulty in using irregular, perishable produce in a timely manner, inadequate communication between buyers and producers both pre- and post-harvest, and discrepancies between the price producers need to receive for their products and buyers’ budget limitations for purchasing unprocessed produce. Several of these barriers can be overcome with “light processing,” defined here as drying, cutting, and/or freezing vegetables.
In the past several years, at least four Vermont businesses and nonprofits increased their investment in processing facilities, but have struggled to expand to appropriate product volume and staff capacity levels and to create a year-round, profitable business model. Food processing facilities face considerable workforce shortages, high start-up and scale-up costs, and challenges navigating food safety regulations, efficiency of scale, and distribution logistics, all limiting the growth of existing and potential for new processing ventures.
Developing a thriving local processing system requires investment in processing facilities, improved communication and commitment between producers, processors, and buyers, and thoughtful workforce recruitment and retention.